- Global
- English
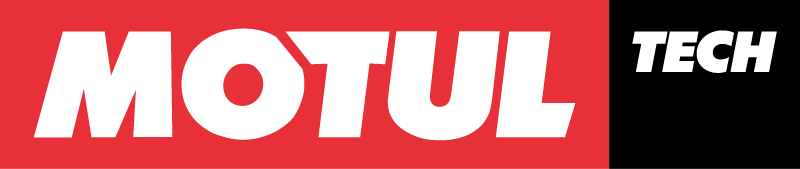
MotulTech designs and manufactures degreasing solutions based on detergents, ready-to-use aqueous cleaners, and solvents tailored to a wide range of industrial needs. These products are used for various cleaning operations: degreasing at the start of the process to remove anti-corrosion protection products, degreasing between machining operations, final precision cleaning, high-pressure degreasing, immersion or ultrasonic cleaning, degreasing before and after heat treatment, desoxidation, descaling, as well as A3 solvents specifically designed for hermetically sealed vacuum washing machines. The company also offers a wide range of products for the maintenance, decontamination, and cleaning of industrial workshops and equipment.
In addition to degreasing products, Motul provides washing equipment such as biological parts washer, dosers, oil separators, and a complete range of services for monitoring your baths.
Degreasing metal surfaces is an essential and crucial step to ensure the quality of the final product by eliminating all substances and particles that could interfere with subsequent production stages. Different types of cleaners are used depending on the materials, technical constraints, type of contaminants, and specific goals of the manufacturing process.
Before carrying out heat treatment or surface treatments such as chrome plating, galvanization, or powder coating, it is critical to thoroughly degrease the parts to remove all organic or inorganic contaminants. Residues can alter heat uniformity and cause defects on treated parts or interfere with the adhesion of coatings. Thorough degreasing not only ensures the quality of the treatment but also its durability.
During part manufacturing, repeated degreasing may be necessary between different machining stages. Metals can accumulate residues such as cutting oils, protective products, soap, phosphates, etc., which need to be quickly removed to maintain the precision of subsequent operations.
Solvents are used to dissolve stubborn oils and greases, which are often present after processes like turning, milling, or turning. Composed of non-polar molecules, solvents can break down organic contaminants and allow for fast and intense cleaning.
Detergents or cleaners can also be used. These solutions must account for the nature of the parts to be degreased (plastic, aluminum, cast iron, etc.), the contaminants to be removed, and the industrial process to offer, if necessary, temporary corrosion protection and optimal cleaning quality. The nature of the detergent (acidic, neutral, alkaline) is critical to the degreasing operation, whether it's desoxidation, dephosphatation, decarbonization, or removal of mineral residues. Depending on the equipment, other factors, such as foam resistance in the case of spray washing or the release capacity to remove foreign oils, must also be considered to optimize cleaning performance and extend bath life.
A3 solvents, used in hermetically sealed vacuum washing machines, offer a significant advantage : they can be redistilled, meaning they can be regenerated for multiple cleaning cycles. These organic solvents, primarily hydrocarbons or modified alcohols, have a narrow boiling range and high stability, which facilitates their regeneration through distillation.
They are widely used after turning, stamping, or machining operations across various industries such as medical, aerospace, watchmaking, automotive, and electronics. Their effectiveness allows for efficient degreasing of parts by removing whole oils, soluble oils, and polishing pastes, while ensuring fast cleaning cycles. Thanks to their low surface tension, these solvents can also effectively degrease hard-to-reach areas such as gaps and threaded holes.
The choice of A3 solvent mainly depends on the type of washing machine used as well as the contaminants to be treated, in order to optimize performance and solvent lifespan through effective regeneration.
Among the products are :
SAFCO KLEEN V, a hydrocarbon-based solvent ideal organics contaminants, offering excellent stability in closed-loop systems.
Metal degreasing is an essential operation to ensure the quality, precision, and durability of industrial parts. Regardless of the metal or equipment used, it is crucial to choose the degreasing method best suited to each situation. MotulTech offers a full range of cleaners covering all cleaning methods: immersion, ultrasonic, and/or high-pressure spray. To ensure an optimal process, in-depth knowledge of the materials and available techniques is often necessary. If you have questions or would like to discuss the best degreasing solutions for your production, feel free to contact us.